AB-INBEV
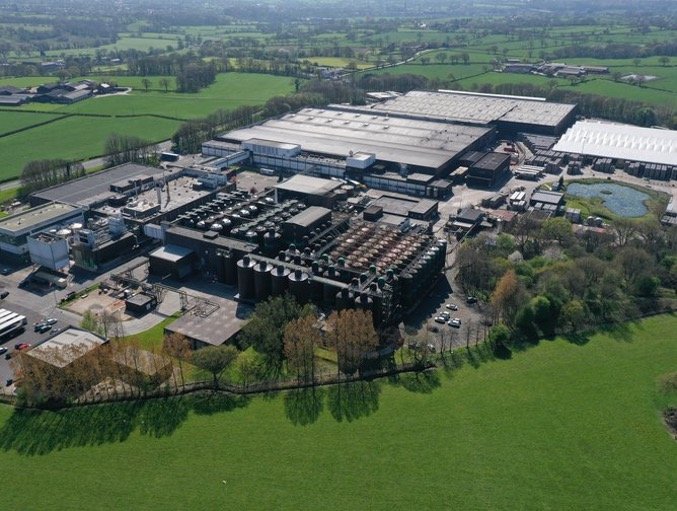
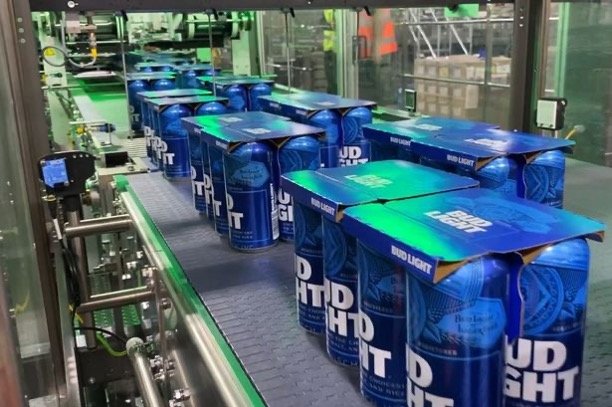
Anheuser-Busch INBEV
FMCG Project
CLIENT NAME Anheuser-Busch INBEV
SCHEME NAME Budweiser Brewery Facility, Samesbury, South Ribble
VALUE £15m
START September 2022
COMPLETION July 2023
PARTNERS RGP Architects, Spring & Co EA, Tier Structural Engineers
PROJECT DETAILS Major Refurbishment and Extension Works to Budweiser’s main brewing plant in the UK. Construction works involved internal demolition, structural steel frame and steel drainage system together with external concrete and resin cladding to the facade.
TESTIMONIAL Paula Lindenberg, president of Budweiser in Britain and Ireland, said: "We know the beer industry is hugely valuable to the UK economy and we believe our investment in our UK operations will be a catalyst for the recovery post-Covid."
Lord Gerry Grimstone, Minister for Investment, said: “Budweiser Brewing Group’s investment is great news for Lancashire, supporting local jobs and helping the nation build back better from Covid-19 crisis. The UK remains extremely attractive to international investors and this investment is further testament to our fantastic beer industry.”
BRIEF 5.5 acre site requiring facility expansion to create a 28,000sqft tented storage and distribution warehouse together with external landscaping for 70 HGV Trailers and widening internal site road and yard areas. This investment is part of a £117m growth plan for its 2 main UK factories boosting beer production by more than 630 pints a year.
SOCIAL VALUE 32 new jobs will be created in the brewing and manufacturing sector making AB Inbev one of the most appealing employers in Preston adding to their 500-strong workforce out of Samesbury.
CHALLENGE: LIVE & FULLY OPERATIONAL MANUFACTURING ENVIRONMENT
Construction works included demolition of existing walls and ceilings to allow for new build extension works to take place.
ACTION:
Sealed partitions, insulated wall panels and temporary screens were used to segregate construction works from brewing facilities
Water Suppression Systems were used to control dust and prevent transfer
Noise suppressors were used on plant and equipment
The Hargreaves team switched to electric vehicles to prevent exhaust fumes on site
Our PM carefully managed daily interaction between facilities management and shift managers ensuring the daily activities were discussed with AB Inbev prior to works commencing so there were no surprises
The project required collaboration and teamwork between all parties and intricate logistics planning
OUTCOME The client’s ER’s including specific hygiene and safety standards were strictly adhered to in order to preserve the integrity of the brewing process.